Efficient Way To Monitor Construction Progress
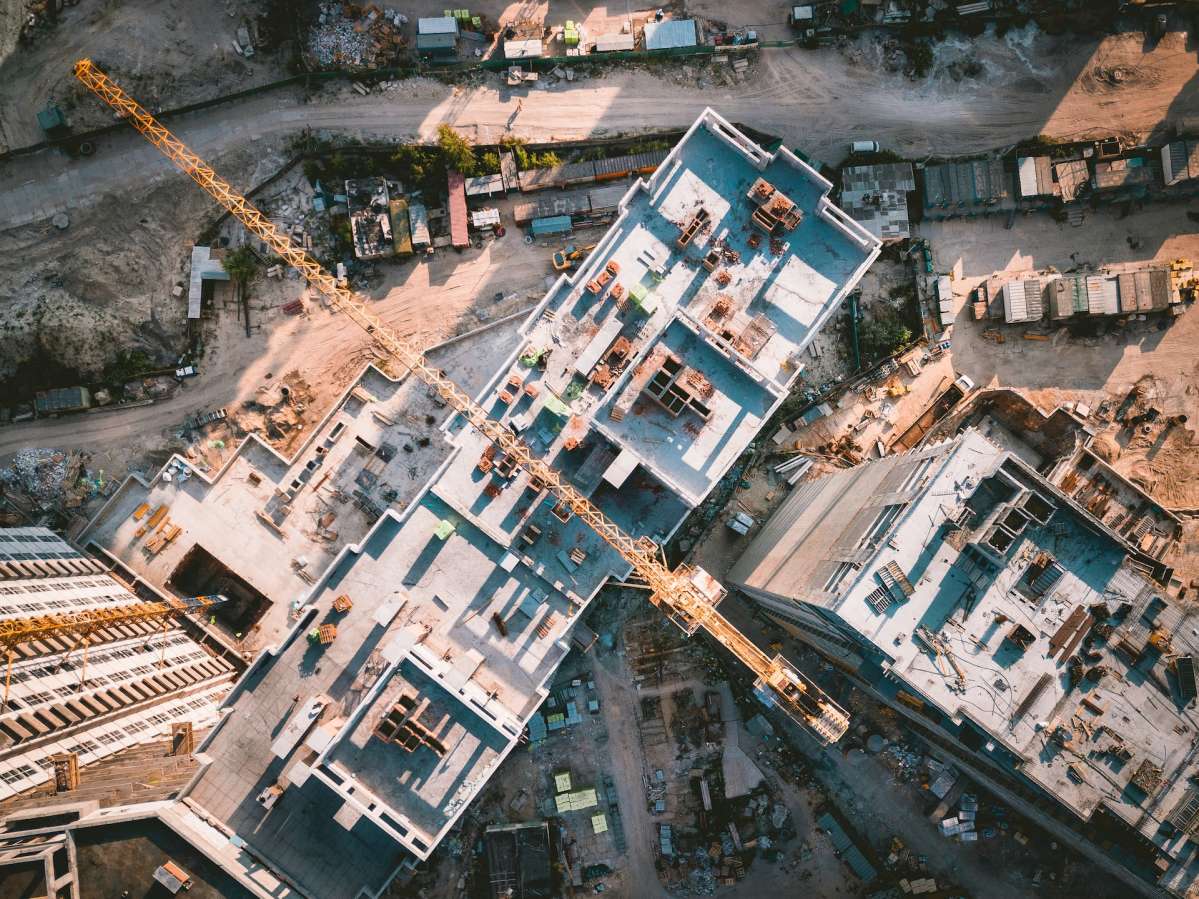
Drone solutions offer a more efficient way to monitor construction progress, reducing costs and time spent on rework. This is accomplished through advanced data collection, accurate mapping, 3D modeling and more.
Physical progress monitoring in construction is traditionally performed through site photography. This article proposes a strategy to perform repetitive structure inspection with UAV and a methodology to compare the reconstructed reality models in coordination software.
Site Inventory
Construction site monitoring with drones helps to provide an accurate and up-to-date inventory of materials. It also aids in the planning and monitoring of the construction process, as well as ensuring compliance with all relevant regulations throughout the project lifecycle.
Drones enable key stakeholders to quickly and easily gather information about the site from any location with internet access. This eliminates the need to travel on-site or hire a prohibitively expensive helicopter. In turn, this cuts costs and speeds up overall project times.
In addition, with the use of drones, a topographical survey is often performed before beginning any work on a construction site. This enables the generation of digital surface models (DTM) and digital terrain maps (DSM) that can then be used for construction planning and design purposes.
This enables the construction team to gain a better understanding of the site conditions, which in turn can help ensure that the building will be constructed as designed and will function as intended. It can also highlight possible drainage points or areas of ground that may need to be leveled before the construction of the building commences.
Drone data is also valuable in determining whether any of the existing infrastructure on a construction site will be affected by the new building. This is often a crucial aspect of the feasibility of a building project, and can be very costly if not addressed early in the planning phase.
It is also a useful tool for calculating the amount of materials that will be required to complete the construction of a building. For smaller construction company’s, this is an important step in ensuring that they have enough material on hand to meet their obligations and timelines.
Finally, the availability of updated and granular site views through drone data can assist in reducing equipment theft on construction sites. This is a huge problem in the industry, and has cost companies billions of dollars. It is much more cost-effective to have a drone monitor the site on a regular basis and generate up-to-date photos than it is to hire security guards.
Volumetric Estimation
Using drones for volumetric measurement is a repeatable and more accurate process that can be completed with less risk than manual methods. Using photogrammetry or LiDAR sensors the drone collects overlapping images/point cloud data of the stockpile or feature whose volume needs to be measured. These are then processed by the software to calculate the volume. This process is very similar to the 3D modeling method but can be performed without the need for a survey crew and the time-consuming ground measurements.
The ability to rapidly capture a complete site area allows for a quick and precise inventory of the material present at any point in time. This provides project managers with a detailed view of the work being done and allows for more realistic planning, estimations and tracking of progress. Drones can also be used to monitor large areas that are otherwise difficult or dangerous to access. This is particularly important in the case of monitoring large infrastructure like railway tracks, water retention basins and solar farms.
In oil and gas, the production of hydrocarbons is largely controlled by the formation volumes of a field. These are estimated by measuring the fluid composition, reservoir pressure (if known), temperature and depth. These estimates are important to the future value of a company as they can be used in forecasting and predicting production rates. Deterministic methods are used to estimate the formation volume of a field while probabilistic methods use predictive tools, statistics and analogue field data to express uncertainty in these estimates.
For construction, drones can provide a fast and precise measure of cut and fill volumes on a daily basis allowing for more accurate project costing and logistics. This helps avoid lengthy disputes at reconciliation when claims are made of earth moved and enables more efficient site operations.
Accountability and theft prevention are also facilitated with regular granular views of the worksite. This prevents the loss of equipment and saves on replacement costs.
Up-to-date drone views can also be shared instantly with all stakeholders irrespective of their location onsight. This cuts down on meetings and travel expenses, allowing project teams to make informed decisions in much shorter timeframes. At Wolfe Remote, progress monitoring with drone technology is a cost-effective solution for all types of construction projects. With its customizable delivery options, repeatable data collection, and automated processes, this is one of the best solutions for progress monitoring in the modern world. Visit Website to learn more about how drone technology can benefit your business.
Site Inspection
The accuracy of drone data and the speed at which it can be gathered, processed, and shared make it ideal for monitoring progress. The ability to provide key stakeholders with the same view of a project that inspectors see on site saves time and travel costs, prevents miscalculations from going unnoticed, and cuts down on costly delays.
Thorough – Areas that are dangerous or difficult to traverse on foot pose little problem for a drone, eliminating the need to send personnel into risky areas to conduct inspections and surveys. This increases productivity by freeing up valuable labor hours for more productive tasks and cuts down on the cost of safety protocols. Reliable – New drone images are captured at regular intervals, offering a consistent perspective and location each time. This makes it easy to compare work done over time, eliminating the need for lengthy discussions at reconciliation periods over disputed claims of earth moved or concrete poured.
Accurate – Drone photos are geotagged and automatically corrected during post-processing to yield a highly accurate orthomosaic map of the construction site, providing 2D geo-information and measurements to directly procure stockpile sizes, road-grade checks, design conformance checks, and volumetrics. These maps can also be overlaid on project designs and blueprints to track progress and help keep jobs on schedule, avoiding costly project delays.
Quick – Drones can fly regularly at speeds that are much faster than a human inspector, making the process of gathering site inspection data very rapid and efficient. A complete drone survey can be accomplished in just a few minutes, and the data can be instantly shared with those who need it. This eliminates wait times, improves communication, and allows key stakeholders to stay involved in projects that they might otherwise have to miss or delay due to a lack of on-site access.
Often, key stakeholders are not situated on-site and may not even be in the same city or country. The availability of up-to-the-minute drone construction site imagery can be a vital tool for keeping investors informed and cutting down on costly project delays. Whether through 3D models, Orthomosaic maps or photogrammetry, the information gained can be used to create acknowledgement reports that are easily accessible and understood by key stakeholders and clients alike.
3D Modeling
For construction teams, having a clear visualization of their projects is essential to ensure quality and productivity. It allows them to identify any potential issues that could arise on the job site and mitigate them before they become a problem. One of the best ways to do this is to utilize 3D modeling. This is done by capturing images and data from the drone and using them to generate digital models of the structure being built. This digital model can then be compared to the as-planned model in a coordination software program to detect any deviations.
This methodology combines the use of three technologies, the UAV, photogrammetry and 4D BIM models, to address the shortcomings that have been identified in the literature regarding physical progress monitoring on construction sites. A standard for UAV operations on the construction site is proposed, allowing to generate useful assets that allow to register, measure and communicate physical work completed on-site.
The methodology provides an orderly strategy for the repetition of UAV flights over the construction structure and the generation of a photogrammetric deliverable that can be used to check physical progress in the site. The reconstructed reality model can be directly compared to the as-planned model in the coordination software, identifying differences between the programmed construction status and the actual state of the structure at the time of the UAV inspection.
Drones are a great tool to use for progress reporting because they can quickly capture aerial images of the project and provide accurate and detailed information about the site. This information can then be used to create reports that can be shared with stakeholders and investors. Consistent monitoring of a construction project can be difficult to do on a regular basis, but using drones to get progress photos regularly makes the process easier and more efficient.
Another advantage of drones is that they can easily be operated by anyone who has a basic knowledge of how to operate them. This allows a single person to perform the progress monitoring instead of requiring multiple people to be at the construction site. This reduces the costs of labor and improves the efficiency of the construction process. In addition, the ability to store the drone data in a cloud storage system makes it easy for multiple users to access the information.
Drone solutions offer a more efficient way to monitor construction progress, reducing costs and time spent on rework. This is accomplished through advanced data collection, accurate mapping, 3D modeling and more. Physical progress monitoring in construction is traditionally performed through site photography. This article proposes a strategy to perform repetitive structure inspection with UAV and…
Recent Posts
- Comprehensive Pest Control Services by Seaside Pest Control in Vancouver, BC
- Azteca Towing Announces 24-Hour Towing Service in Phoenix
- How Professional Tree Stump Removal Services in San Diego Minimize Risk
- Affordable Fencing Solutions: Fence Company Rochester NY Offers Insight on the Cheapest Fence Installations in Rochester, NY
- Affordable Fencing Solutions: Fence Company Rochester NY Offers Insight on the Cheapest Fence Installations in Rochester, NY